Coatings Technology Blog
When Mold Release Agents Failed for Stator Manufacturer, Nedox Provided a Clean Break
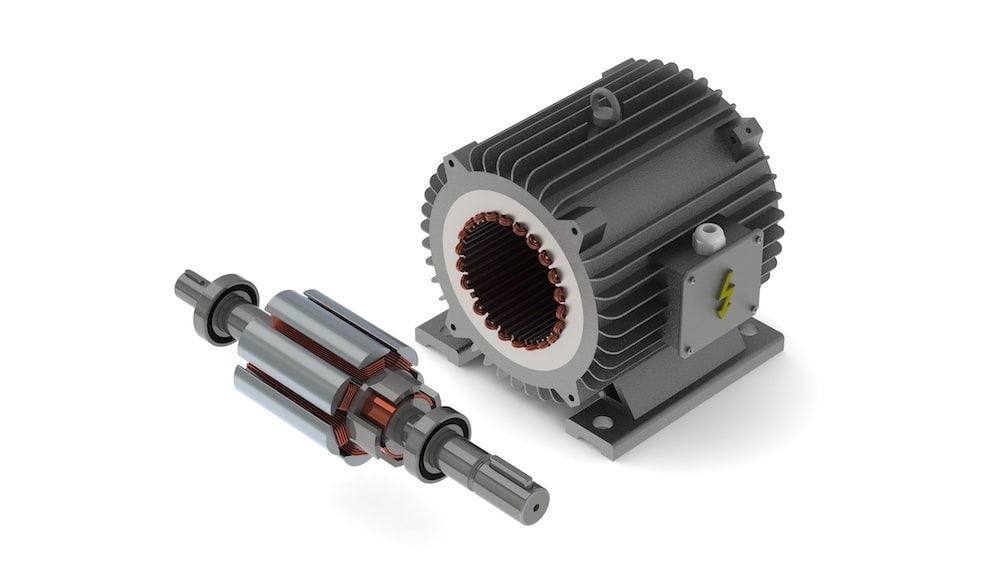
A stator is the stationary part of a moving system, such as a motor. In fluid-powered mud motors used in downhole drilling, the stator guides the flow of drilling fluid drawn from the surface, converting it into rotational horsepower. Along with the rotor, this creates the torque and rpm to spin a drill bit.
The stator is typically a metal tube lined with an elastomer in a specific formation using an external mold, or negative. The mold is placed inside the metal tube which is also injected with molten rubber, before the entire component goes into an autoclave for curing. After curing the mold is removed, leaving the negative impression and an injection core that holds the rotor during its nutation.
However, freeing the core from the stator tube is no easy task. Rubber often remains stuck to the tube and can damage the stator. Not only does the damage create costly downtime, removal is also difficult and expensive. One recent customer was plating its stator parts with hard chrome and then applied a silicone mold release coating. But after only a couple of uses, this silicone product would build up on the stator tube and actually hamper mold release. Additionally, the caustic compounds within the rubber caused premature pitting on the parts.
The customer gave our technical support team a test sample, which we coated entirely with a nickel-based Nedox® surface treatment. Well-known for its ability to eliminate stick-slip and galling in a wide variety of applications, Nedox helps less-durable materials achieve and surpass the longevity of chrome and stainless steel. We formulated the Nedox coating to provide superior mold release properties along with exceptional hardness and permanent lubricity. Nedox also features:
- Good performance in chemically corrosive environments.
- Excellent salt spray resistance.
- Abrasion resistance.
- A wide operating temperature range of 250 to 1,000°F (-157 to +538°C).
The part immediately went back into service and returned excellent results: It released from the rubber much more easily than any form of chrome and release agent the customer had previously used. The part was also much easier to clean, requiring just a simple wipedown. Months later, the company is pleased to report that the parts are still holding up better than chrome, withstanding the wear and tear of frequent movement around the shop. They also noted that the caustic compounds within the rubber were not damaging the coating.
Magnaplate Coatings Make an Effective Release Strategy
When you’re working with elastomer molds that leave behind stubborn rubber residue on parts, you can’t afford the costs and loss of productivity that result from choosing the wrong release strategy. That’s why our technical support team examines all your application details, helps you determine the best surface treatment option for the job and makes sure it works as intended. This successful application is another example of how a customer not only eliminated mold release issues with a Magnaplate engineered coating, but was also able to protect its parts in a tough downhole drilling environment.
For more information about Nedox surface treatments, visit our product page.