Coatings Technology Blog
Plasmadize® Keeps Metal Extrusion Parts in Good Shape
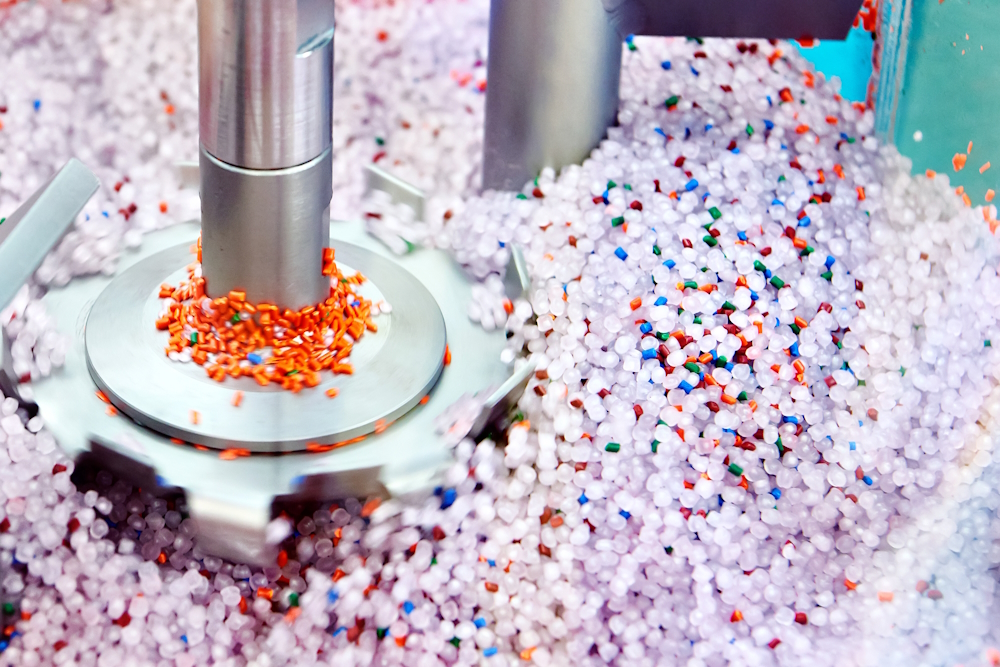
In plastics processing, the quality of the finished product depends on how well the materials are mixed during extrusion. Consistency is crucial: Materials must flow continuously through the extrusion line at a specific rate. The smallest variation in the mixture can alter the product's strength and performance, while any interruptions to the process can be costly. That means metal parts like mixer blades must be properly maintained even under constant operation and exposure to harsh chemicals.
Mixer blades are particularly susceptible to abrasive wear from thick plastics. In no time, they can eat away and bend the blades, causing them to break. In fact, one plastics processor came to us with large steel mixer blades comparable in size to airplane propellers.
In use, the blades were quickly damaged by a very thick abrasive plastic, and replacing them was prohibitively expensive. This Magnaplate customer unsuccessfully tried to repair them by welding the cracked and broken areas. By the time we received the blades, they were beat up and too caked with hardened plastic to allow us to fully see their poor condition until we cleaned them. Blasting removed much of the welding and revealed extensive damage.
After another round of repairs, we were able to apply a Plasmadize® surface treatment to the mixer blades. This enhanced thermal spray composite features exceptional wear resistance, is especially desirable for rebuilding and restoring old worn parts, and resists harsh chemicals. The composite materials in Plasmadize are applied either simultaneously or in as many as three sequential process steps.
Thanks to this unique approach, a structurally stable surface is created, providing greater wear resistance than chrome plating or heat-treated electroless nickel without the brittleness and porosity of conventional thermal sprays.
Plasmadize Technical Advantages
Our standard Plasmadize coatings thickness is .003 to .005 inch, but it can be modified depending on the application requirements. The new surface can then be precision-ground or machined back to specific, close tolerances. In addition to restoring parts to "better than new," Plasmadize can also be applied cost-effectively to very large surfaces or parts — such as our customer's mixing blades.
Additional features and specifications include:
- Hardnesses beyond the Rc scale.
- Low coefficient of friction (CoF).
- Equilibrium wear rate (EWR) as low as 0.1 mg per 1,000 cycles.
- Resistance to acids, alkalis, chlorides, most organic solvents, sulfites, thiosulfates and pulp bleaching chemicals.
- Operating temperatures from -200°F (-129°C) to +1,300°F (+704°C).
Ideal for Extrusion, Mixing Equipment and More
Our customer decided to try Plasmadize for one month to evaluate its efficacy. They advised us that the uncoated blades wore out significantly faster than the Plasmadize-coated blades. Pleased with this success, they delivered many more blades to us for treatment with Plasmadize.
When metal parts used for extrusion, mixing, feeding, crimping, conveying or tensioning require optimal wear protection or simply need new life, we stand ready to help you select an ideal Plasmadize composite for the job.
For more information about Plasmadize, please visit our product page.