Coatings Technology Blog
Nedox® Holds the Line on Brine in Hydrocarbon Reservoir
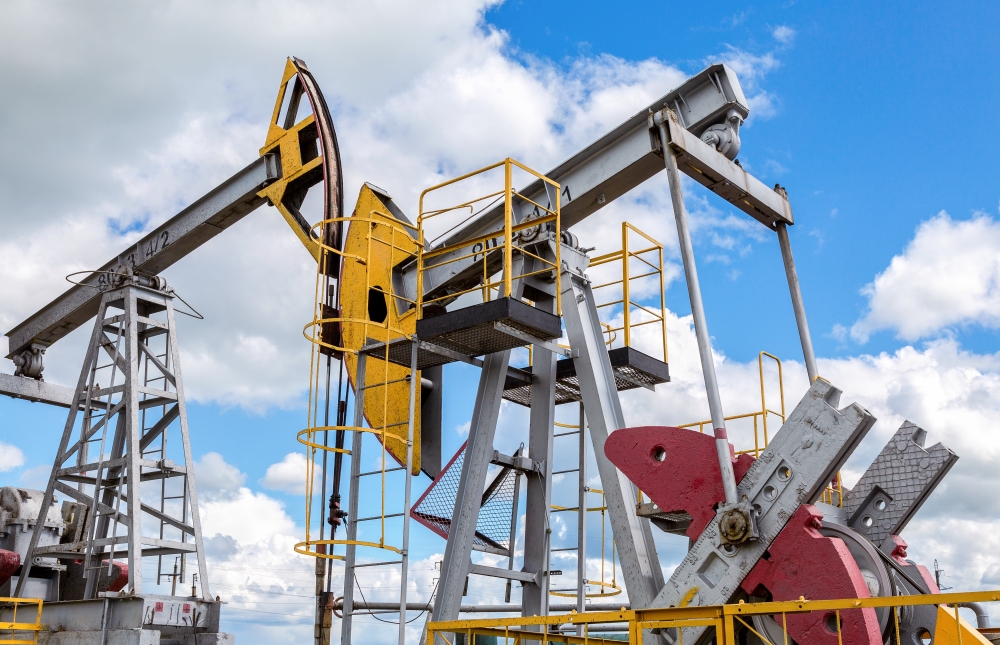
It’s no secret that oil and gas facilities pose some of the toughest conditions that metal parts can endure, and wells that extract oil from hydrocarbon bearing formations are among the harshest sites. Inside these wells, parts such as pumps typically encounter produced water. Sometimes known as “brine” or “formation water,” produced water exists in underground formations and is brought to the surface along with oil or gas during production activities. This blog post will describe how Magnaplate was able to help a builder of pump packages protect its metal components in a punishing oil reservoir.
This Magnaplate customer designs and engineers pump packages and turnkey facilities for leaching systems, water disposal systems, water flood systems and main line systems. They work with several OEM pump manufacturers and can repair a variety of pump, compressor and well servicing equipment. Recently, the company took on an application that involves produced water that has been in contact with a hydrocarbon-bearing formation for centuries. The water may include water from the reservoir, water injected into the formation, salts, oil, grease, dissolved solids and any chemicals added during production and treatment processes. Taken together, these constituents make metal parts particularly vulnerable to corrosion and abrasion.
Our customer asked us for a coating with good corrosion and abrasion resistance properties that would protect steel end plates, rotors, housings and spacers in pump packages that will be exposed to produced water from the hydrocarbon-bearing reservoir. We recommended a Nedox® surface treatment that is particularly effective against corrosion and abrasion. Not only has this electroless nickel coating proven highly resistant to salt spray, it also offers exceptional resistance to chemicals, acids and alkali. The Nedox family includes many variants that employ various polymers, dry lubricants and other materials to achieve different properties like enhanced hardness. Additional features and characteristics include:
- Surface hardness up to Rc 68.
- Self-lubricating for extended wear protection.
- Operating temperature range of -250 to +1,200°F (-157 to +649°C).
- Compliant with ASTM B733, ASTM 2404, AMS-C 26074 and REACH.
The first set of parts was tested over a period of six to nine months with great success, resulting in a large reduction in equipment downtime. Since then, we have coated several more sets of parts. This successful application is another example of how Magnaplate engineered coatings have effectively protected metal parts against harsh conditions like corrosion and abrasion in oil and gas installations, giving them a long operating life. A Magnaplate technical sales representative can discuss the threats you expect your parts to face in your oil and gas equipment and help you determine the best coating for the job.
For more information about Nedox electroless nickel surface treatments, please visit our product page.