Coatings Technology Blog
How to Select the Best Engineered Coating for Your Aluminum Parts
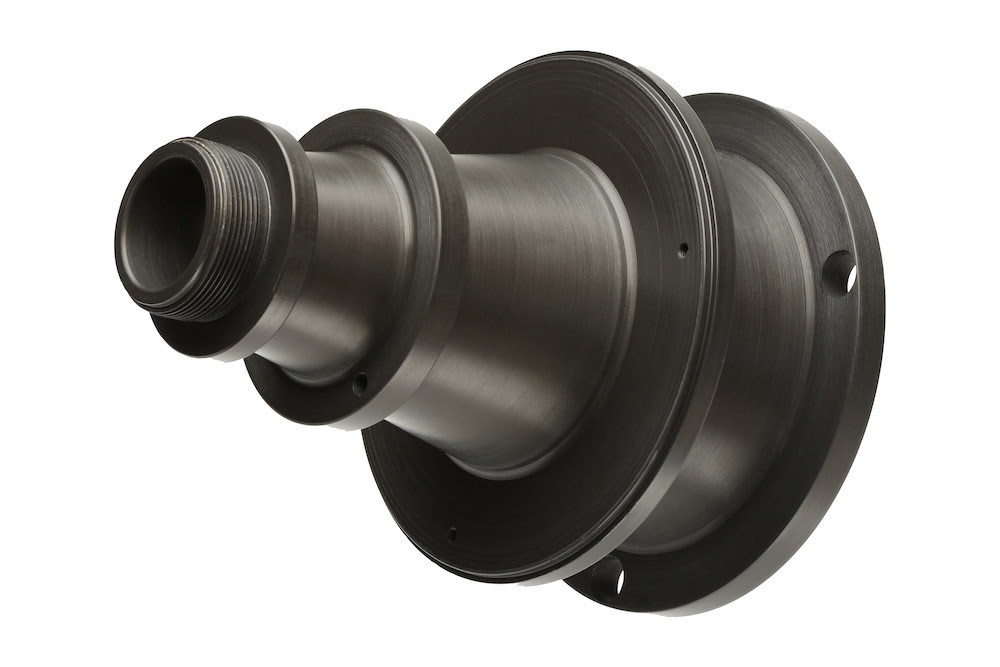
Aluminum is among the most widely used metals for fabricating parts — and for good reason. This low-cost material offers a high strength-to-weight ratio, and its versatility makes it suitable for a wide range of applications. When it comes to protecting aluminum from threats like corrosion and wear, engineered coatings offer many benefits. This blog post will describe some key factors that can help you determine which Magnaplate engineered coating is right for your aluminum part.
Among our lineup of engineered coatings, two families are well-suited for protecting aluminum parts — Tufram® and Nedox®. Since all aluminum parts and their environments are not the same, some applications are better suited for Tufram while others are ideal for Nedox. Here’s a quick overview of their features and advantages in certain situations to help you narrow your selection:
Tufram
These coatings are formulated for aluminum surfaces and outperform conventional hard anodizing and similar processes for resisting corrosion, reducing friction and improving hardness. Consider Tufram when:
- You need electrical insulation. Tufram exhibits good electrical insulation properties.
- You need wear resistance. Tufram's low coefficient of friction protects against abrasive wear mechanisms as well as galling.
- You need to prevent chipping or peeling. Tufram doesn’t flake, chip or peel like paint-on coatings. Instead, it forms an aluminum oxide when applied. The coating becomes an integral part of the base material to form an even greater protective layer.
- When you need cost efficiency. Tufram’s application process is straightforward, making the coating family attractive for applications with budget constraints.
Nedox
Metal parts, including those made of aluminum, receive a harder-than-steel, self-lubricating surface that resists corrosion, friction, sticking, galling and static buildup, improving longevity and part performance. Consider Nedox when:
- You need optimal hardness. Metal parts treated with Nedox become harder than steel. Nedox can achieve Rc 68 (940 Vickers scale), allowing customers to use a less-expensive base material without sacrificing performance.
- You need ductility. Nedox exhibits more ductility than ceramic-based coatings.
- You require greater uniformity. Since Nedox does not rely on electrical current, it achieves uniform thickness. This characteristic makes the coating especially attractive for parts with inner and outer diameters or edges.
- Your aluminum alloy has high silicon or copper content. Nedox is suitable for most of these aluminum alloys.
- You need a tight dimensional tolerance. Since there are no high and low current density areas to create variances, Nedox can achieve tolerances as low as ±0.0001 inch.
A Versatile Material Demands an Engineered Coating
Aluminum is a popular choice for parts, thanks to its light weight and strength. But while it offers great versatility, its many uses can make your choice of protective coatings difficult. Tufram and Nedox engineered coatings are appropriate for a wide range of applications involving aluminum parts. Both coatings have characteristics that make them desirable for certain requirements, and we can modify each one to achieve special performance needs. Be sure to work with us early in the selection process to help you determine the best option for your aluminum parts.
For more information about Tufram and Nedox coatings for aluminum and aluminum alloy parts, contact us.