Coatings Technology Blog
How to Bolster the Benefits of Anodized Aluminum Surface Treatments
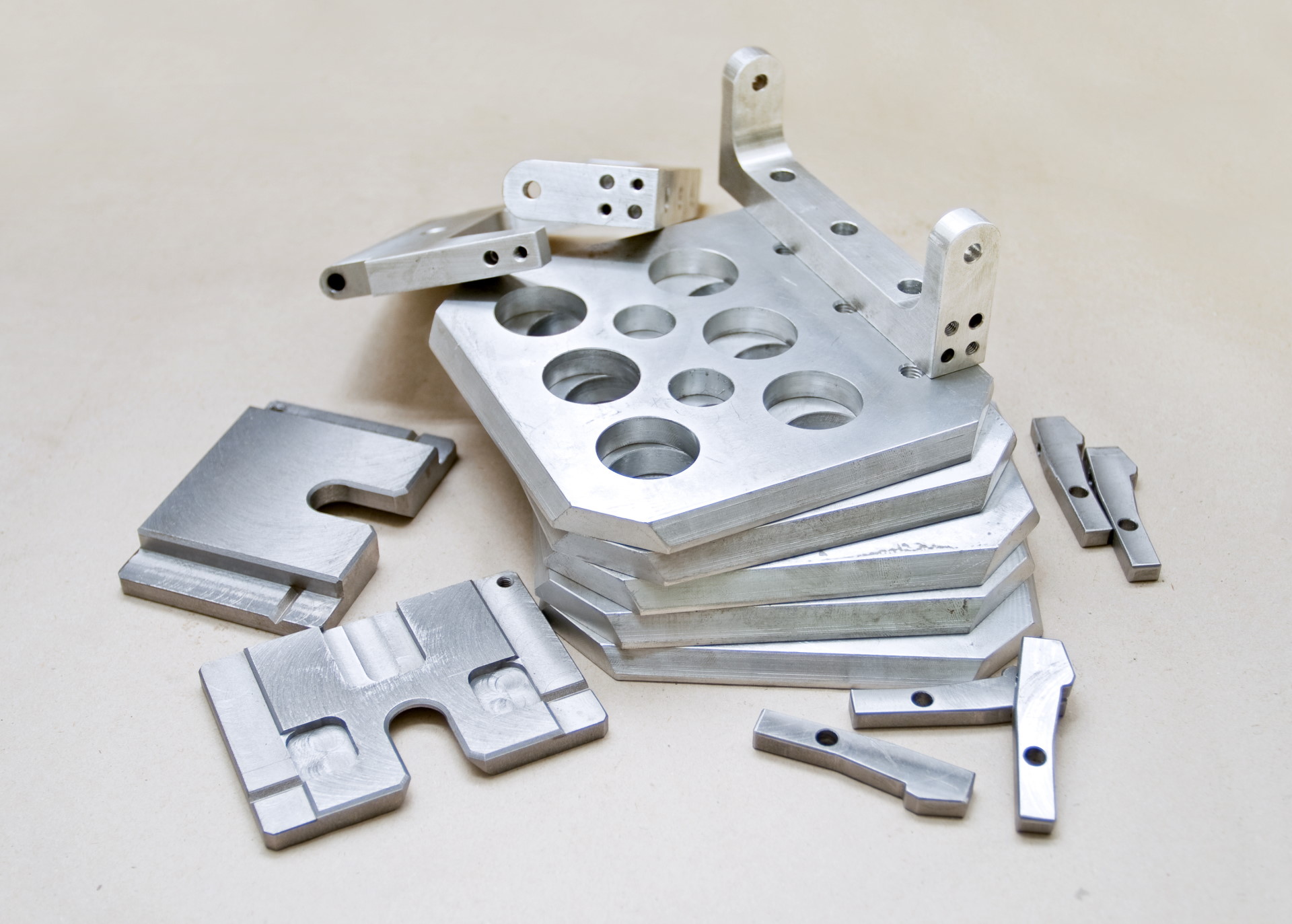
As you consider ways to improve the durability or aesthetics of an aluminum or other nonferrous metal part, anodizing is often a top choice. While anodizing may be the first thought that comes to mind for aluminum surfaces, don’t overlook another option that provides even greater protective benefits than those of anodizing. This blog post will describe how one coating is formulated to deliver greater hardness, corrosion resistance and lower friction compared to conventional hard anodizing processes.
Anodizing: An Overview
Anodizing is an electrochemical process that converts a metal surface into a durable, corrosion-resistant oxide finish. Typically, an aluminum part is submerged in an electrolytic bath while a direct current passes through the solution.
MIL-A-8625 classifies aluminum anodizing processes. Among them, there are three main types of anodizing based on the thickness of the oxide coating: Type I, Type II and Type III. Known as “hard anodizing,” Type III is desirable for applications requiring the highest oxide thickness.
An Engineered Surface Enhancement Coating for Aluminum Components
Although Type III anodizing is generally considered an “engineering hard coat” thanks to its extreme hardness and abrasion resistance, it is possible to obtain even greater protection for aluminum and aluminum alloy surfaces. Our Tufram® coating, with a thickness range of 0.0004 to 0.003 inches, combines the hardness of an aluminum oxide finish with infused proprietary polymers to outperform traditional anodizing processes in several ways:
- Corrosion resistance. Not only are Tufram coatings highly resistant to atmospheric and marine corrosion, some types also withstand acids and alkaline chemicals. In salt spray testing, Tufram on high-strength aluminum exceeds the AMS 2482 requirement of 336 hours, and submersion tests in strong acids at 248°F show no effect after more than 170 hours.
- Abrasion resistance. In tests, Tufram exhibited far better wear resistance than either case-hardened steel or hard chrome plate.
- Hardness. Depending on the Tufram coating and alloy used, surface hardness ranges from Rc 40 to Rc 65 — levels comparable to case-hardened steel or hard chrome plate.
- Lower friction. Tufram’s low coefficient of friction is as much as 50 percent lower than that of hard anodizing. The coating gives the aluminum surface exceptional lubricity and, in turn, superior release characteristics. It also eliminates undesirable vibrations in sliding motion applications.
In addition to improving the performance and durability of aluminum components, Tufram often allows easily machinable aluminum to replace more expensive steel or stainless steel substrates in many applications. Tufram also offers these additional features and advantages:
- Good impact resistance.
- A wide operating temperature range.
- Compliance with FDA/USDA and many military and industry standards.
- Self-lubricating and non-wetting surfaces.
- Excellent thermal conductivity and high dielectric strength.
- Absence of outgassing.
Optimal Protection for Aluminum Parts
When you’re looking to improve the hardness of an aluminum surface and protect against corrosion, wear or abrasion, anodizing is a common first choice. However, your application may require added benefits that anodizing may not provide, or need a higher degree of protection against these threats. Tufram coatings combine the advantages of hard anodizing with engineered enhancements to give your aluminum parts optimal protection and long life. Our experts can help you evaluate your needs and formulate an optimal Tufram coating for your aluminum part.
For more information, visit our product page.