Coatings Technology Blog
How Metal Coatings Give The Dry Bulk Solids Industry An Edge
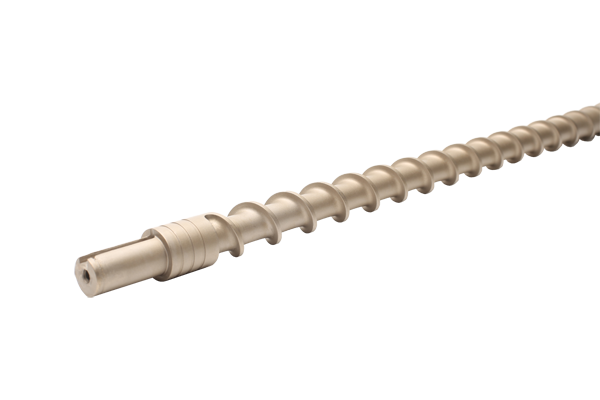
When it comes to bulk solids metering and handling machines, metal coatings play a crucial role. For one, they help reduce friction on metal feeders and prevent sticking. They also protect feeder components from wear. Certain materials, such as metallic powders, oxides and silica-type ingredients, are abrasive—leading to premature wear, part replacement and costly downtime.
Bear in mind, however, that some coatings are better than others. The right coating not only provides the necessary protection but also meets the proper compliances. Here’s a rundown of what you should look for:
- Low coefficient of friction reduces metering errors. Metering, which involves proportioning, blending and hoppering of dry solid ingredients by volume or weight, requires accuracy. Coatings should have a low coefficient of friction, preventing adhesive materials and even dust from sticking to machine parts. Doing so reduces metering errors, which has vast cost implications for companies that use expensive dry solid materials. LECTROFLUOR® coatings help improve sticking issues by providing excellent release properties.
- Meeting federal standards alleviates compliance concerns. Each industry has its own set of unique requirements and federal standards—and coatings need to be in compliance with them. Many of our smart coatings already meet strict FDA and USDA standards, giving them the edge over chrome in food and pharmaceutical applications.
- Corrosion resistance avoids adverse chemical reactions. Materials like chlorides can react with a variety of metals, including stainless-steel, causing corrosion or contamination of handling equipment. For many chemical manufacturing companies, this can be a real concern. TUFRAM® and NEDOX® coatings are designed to resist most common chemicals and salt spray—even after prolonged, continuous exposure.
- Coatings prevent wear. Feeders and other machines are expected to operate on a grueling 24/7 schedule with near-zero maintenance requirements and downtime. The right coating protects components from premature wear, ensuring you don’t have to stop production just to replace a part. For increased wear resistance, coatings like TUFRAM®, NEDOX® and PLASMADIZE® are great options.
In addition to dry bulk solids, you can even use our coatings to treat surfaces that handle molasses-like ingredients. For example, a company that specializes in producing animal feed recently utilized NEDOX® to enhance its manufacturing process. Molasses, which acts as a binder for the feed, was sticking to the mixing equipment. But thanks to its superior release properties and abrasion resistance, our NEDOX 10K-3® coating overcame these issues—preventing sticking and protecting equipment from additional wear.