Coatings Technology Blog
Get the Full Benefits of Extended Wear Protection for Your Metal Parts
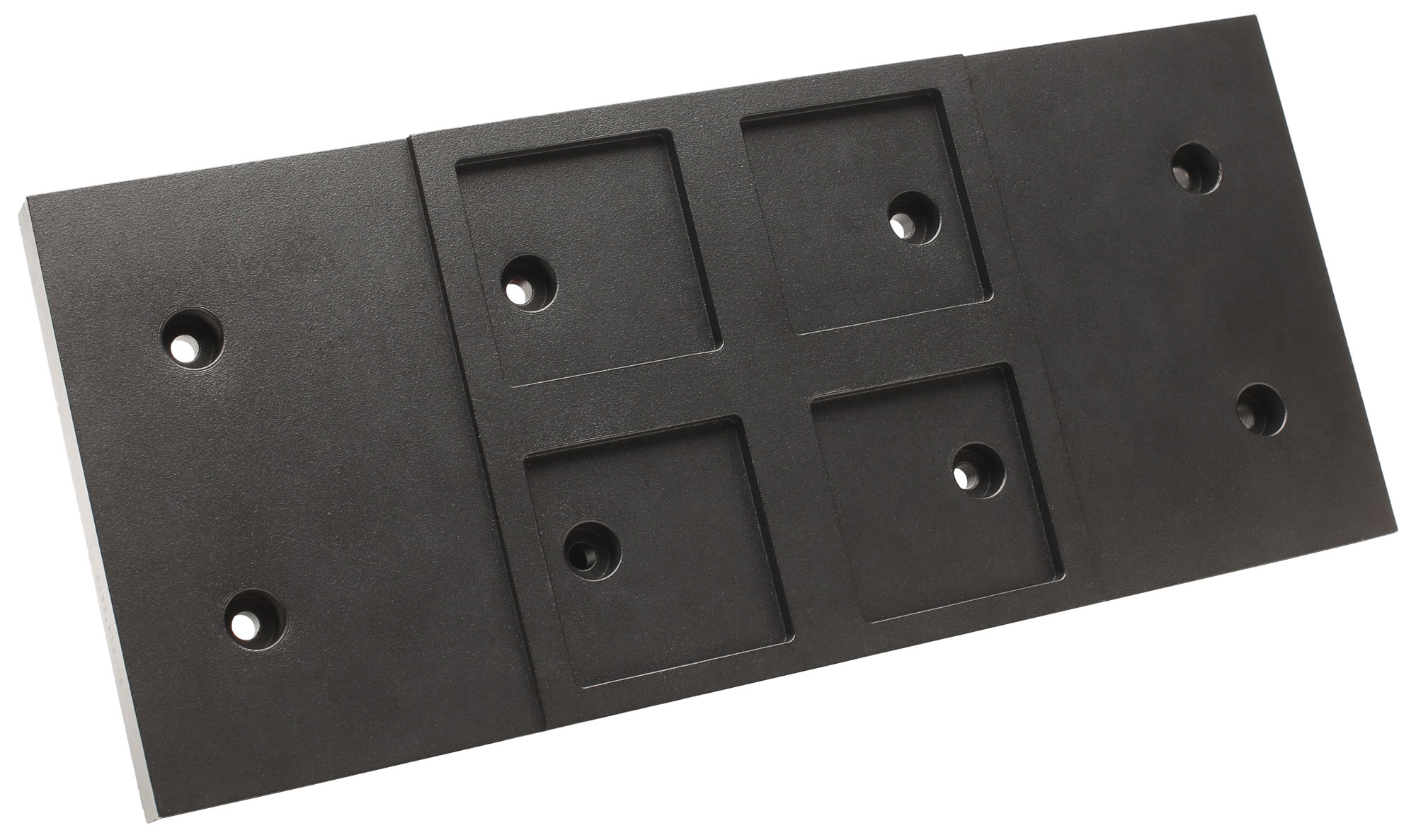
What’s the best way to protect metal parts against wear, abrasion or corrosion to ensure long lifetimes? Engineers evaluating protective coatings for metal components may not be aware of the advantages that thermal sprays offer over conventional coatings. This blog post will focus on some of the benefits of thermal spray coatings as they pertain to common considerations engineers have when they choose a surface treatment, along with tips on how to take full advantage of those benefits.
Thermal Spray Advantages
Thermal spraying protects and restores metal parts by mechanically bonding to the substrate material, altering its surface properties to create a nonporous, moisture-proof, composite coating. Thermal spraying holds up to most extreme wear, corrosion, abrasion and fatigue degradation applications. Thermal spraying is particularly versatile — it can be applied to almost any metal, and it can be customized to a desired thickness, hardness or coefficient of friction.
Among thermal spray technologies, Magnaplate’s Plasmadize® stands out thanks to an infused matrix of metals, ceramics, polymers and dry lubricants that creates structural integrity and a nonporous, moisture-proof surface. Featuring excellent lubricity and mold release, Plasmadize offers a host of features that make it a better choice than conventional coating methods:
- Withstands temperature extremes. Plasmadize thermal sprays perform across a wide operating temperature range of -200ºF (129ºC) to 1,300ºF (704ºC). And, some Plasmadize coatings can continuously operate at up to 2,280ºF (1,249ºC).
- Repair and reapplication. Thermal sprays can outlast the original materials, so repairing a part can be cheaper than buying a new one. Most parts using Plasmadize can be stripped and recoated.
- Consistent application. Plasmadize creates a consistent and repeatable finish. For recurring jobs, Magnaplate deploys programmable robots to ensure consistency every time.
- Protection for steel. When steel encounters spinning parts, it is prone to cutting. Thermal sprays like Plasmadize are engineered to protect steel along with many other substrates.
- Additional features and benefits:
- Thickness from 0.003- to 0.25-inches.
- Equivalent Rc of 72.
- Resistant to salt spray.
- Coefficient of friction as low as 0.13 on an 8 RMS surface.
- Suitable for a wide variety of applications including food and pharmaceuticals.
Extend the Benefits of Thermal Spray Technology
Magnaplate works closely with customers and controls a number of variables to produce different enhancements based on a customer’s individual coating needs, particularly for adjustable requirements like friction, wear and desired hardness. That includes raising or lowering thicknesses with tolerances down to thousandths of an inch, and some surface depositions can be ground to ±0.0001 inch. Coatings can be customized to satisfy specific requirements, with either a ceramic or metallic base, and an appropriate dry lubricant or polymer for the application. The polymer infusion gives Plasmadize its excellent release properties with heat dissipation and low coefficient of friction characteristics.
When you choose thermal sprays to resist wear, corrosion and fatigue, you’ll get several performance benefits that make them the better choice versus conventional coatings. Magnaplate’s Plasmadize composite coatings combine the advantages of thermal spray technology with custom enhancements to make sure parts achieve optimal protection and long life.
Find out more about Magnaplate’s Plasmadize thermal spray composites.