Coatings Technology Blog
Engineered Coatings Optimize Powder and Bulk Solids Equipment Output
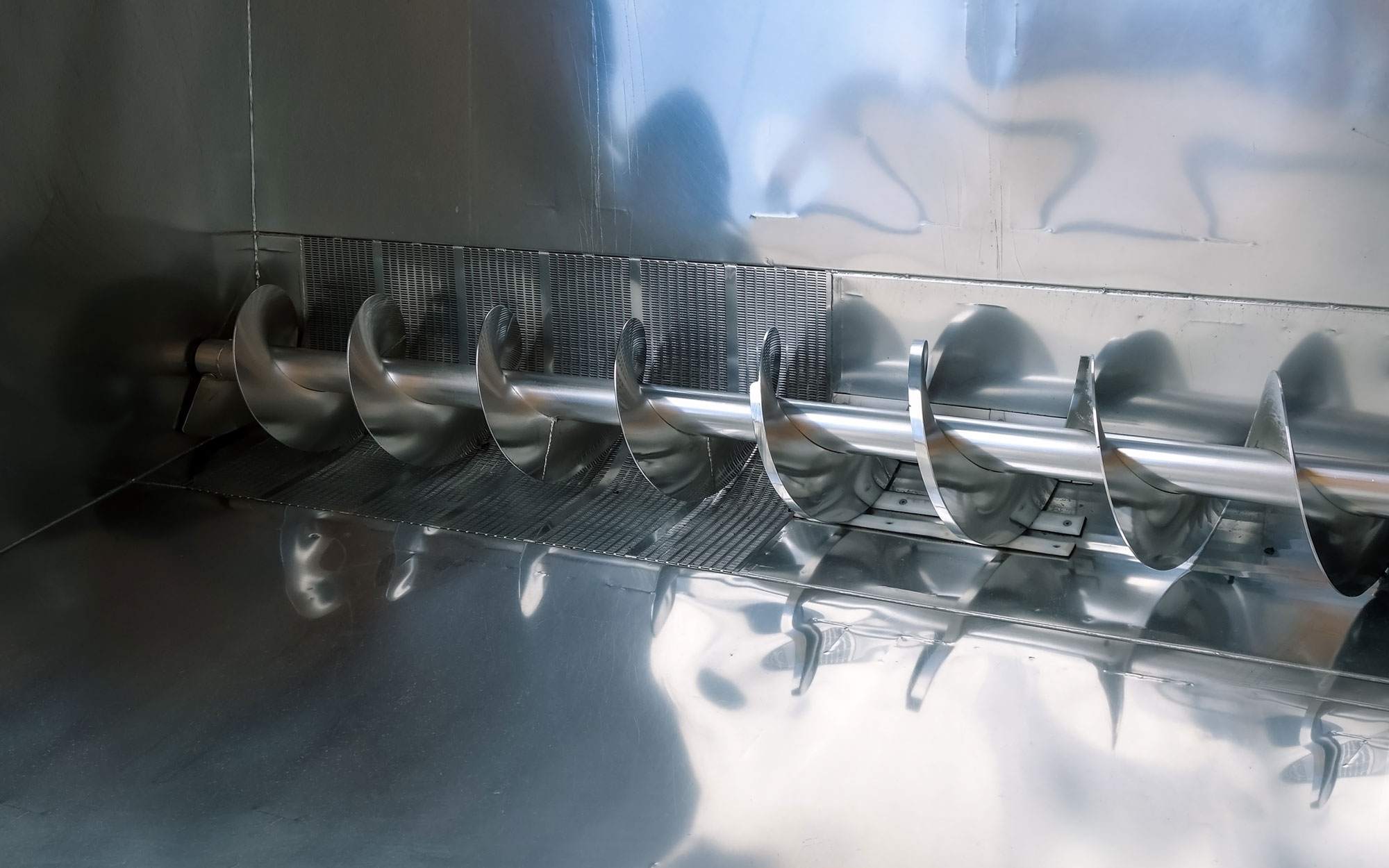
In the powder bulk solids industry, precise metering and efficient material feeding are critical. However, several conditions can hinder machine performance and affect lifetime. In order to avoid unwanted downtime or premature replacement, protective coatings are a must. Powder and bulk solids handlers typically have three main concerns:
- Wear and abrasion. Because hard materials are broken into smaller particulate materials, friction is a natural threat to the lifetime of a substrate. Wear is a common problem in feeder components used to transport dry materials.
- Corrosion can result from various conditions. Despite being particulate in nature, the material may still contain moisture. Chlorides can react with a variety of metals. The equipment may operate in a humid environment. Add to that, cast materials may be porous.
- Preventing sticking. Sticky materials may clump or bridge, hindering their flow through meters or congesting filters or screens.
Because powder and bulk solid applications can present a variety of challenges, it pays to protect equipment with coatings that can address specific conditions for each application. Magnaplate offers a lineup of proprietary coatings that can be engineered to address wear, abrasion, corrosion, sticking and other concerns. Highlights include:
- Tufram® coatings protect aluminum against corrosion, offer a low coefficient of friction to help reduce heat and wear, and can resist common chemicals found in powder and bulk solids applications. It exhibits non-stick properties as high as 850°F (454°C).
- Nedox® is especially suited for stick-slip prevention and offers surface hardness up to Rc 68 (940 Vickers) to protect against wear. It performs well against friction and corrosion, and it also exhibits good chemical, acid and alkaline resistance.
- Lectrofluor® polymer-based coatings for harsh environments can be engineered to address a wide range of conditions. Depending on the end use, Lectrofluor can be engineered to provide a low coefficient of friction, resist chemicals, acids and alkalis, or to ensure mold release and reduce sticking.
- Plasmadize® enhanced thermal spray composite coatings resist abrasion, corrosion, and many chemicals, acids and alkalis. It also seals surface voids to eliminate porosity and can perform at temperatures as high as 525°F (274°C).
In addition to their protective features, many Magnaplate coatings comply with strict industry standards including FDA and USDA regulations.
Engineered Coatings Produce Quality and Consistency
Magnaplate’s technical staff can review your application information and suggest a coating that best matches the conditions affecting your equipment. The resulting coatings can be applied uniformly every time regardless of the part’s geometry, and they may even enhance the characteristics of the substrate. When it comes to powder and bulk solids, Magnaplate engineered coatings can help ensure your end product has consistent quality.
For more information about Magnaplate engineered coatings for the powder and dry bulk solids industry, visit our industries page.