Coatings Technology Blog
Engineered Coatings Boost Productivity in Automated Systems
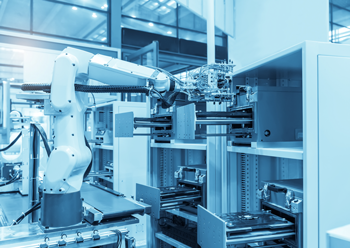
To reap the benefits of automation, your equipment—from robotic systems to packaging machinery—must continue running at high speeds. For this reason, it’s important to identify and mitigate troublesome issues like abrasion, premature wear, corrosion and sticking. One way to overcome these challenges is by using engineered coatings.
In a new white paper, we explore how these coatings work, as well as the ways they solve common performance problems in high-speed automation applications:
Overcoming Common Machine Problems
Engineered coatings permanently enhance the surface of metals and other substrates used in automated machinery to solve corrosion, wear, lubrication and release problems. For example, sticking is a common problem in heat-sealing equipment. As polyethylene film strips melt together to seal a package, the melted material and adhesive glues can stick to seal bars. In robotic systems, metal-on-metal contact between steel parts running at high speeds also creates tremendous friction forces—leading to premature wear.
To solve these and other challenges, Magnaplate has developed custom coating processes. For example:
- NEDOX® is a nickel alloy-based coating that protects aluminum and other metals against wear, corrosion, sticking and galling. Within the NEDOX® group are several options that use various polymers to impart specific properties, such as enhanced hardness, superior mold release or easy release at high temperatures.
- The TUFRAM® line for aluminum and aluminum alloys also features a range of formulas suited to a variety of applications.
- GOLDENEDGE® keeps cutting surfaces sharp and extends their life up to 20 times. This coating formula may be used alongside other coating families.
To learn more about our engineered coatings in automation applications, download our latest white paper