Coatings Technology Blog
Embroidery Machine Builder Overcomes Corrosion and Wear Issues Using Our Coating
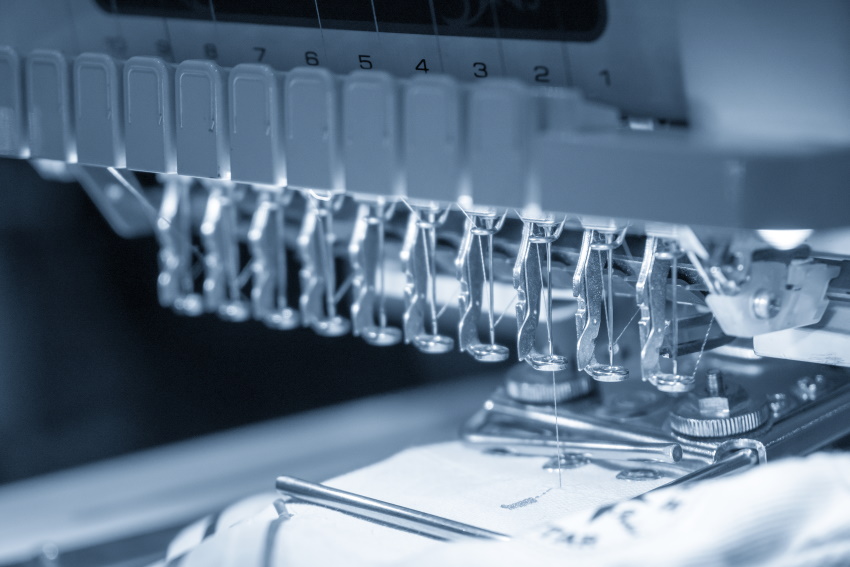
For many industrial engineers and plant managers, ensuring lasting machine performance often hinges on corrosion and wear prevention. Engineered coatings protect metal components from the effects of moisture and wear to solve performance and longevity problems for a wide range of industries and applications. These specialized coatings infuse polymer particles into substrates to create mechanical bonds that permanently enhance the surfaces of metal parts. This process imparts hardness, dry lubrication and chemical and corrosion resistance characteristics so the parts are more reliable, last longer and are more cost efficient.
At Magnaplate, we produce a broad range of coatings to satisfy even the toughest metal performance requirement. Virtually any piece of industrial equipment can benefit from a carefully specified coating applied to machine parts where problems are known to occur. Examples of some of our coatings that provide corrosion and wear protection for a wide variety of substrates are Nedox®, Plasmadize®, Tufram® and Dynaloy®, our ultrathin chrome process. In addition, Lectrofluor® is formulated to prevent severe corrosion, Canadize® protects titanium parts from wear and abrasion and Magnadize® provides wear protection for magnesium components.
An Embroidery Machine Builder Avoids Corrosion and Wear Issues
Like many other industrial machines, embroidery devices require protection from corrosion and wear. Humidity can cause corrosive moisture to build up on embroidery machine parts, while continuous use and vibrations can cause the parts to wear, shortening machine lifetimes. Without protection, these machines can break down and incur repairs and costly downtime. In addition, corrosion and wear can compromise the quality of the finished products.
These are the reasons why an embroidery equipment manufacturer — whose customers range from small startup shops to large-scale operations that stitch names and logos onto major clothing lines — trusted us to keep a key part running smoothly. The part fits into a machine’s reciprocating assembly that drives the thread through the fabric.
We coated this component with Magnaplate HCR®. This engineered coating produces a harder-than-steel surface on aluminum parts, offering greater corrosion protection and wear resistance properties than conventional hard anodize. Magnaplate HCR complies with MIL-A-8625 and ASTM B-117 requirements, and it can withstand salt spray exposure in excess of 15,000 hours — easily exceeding the MIL-SPEC of 336 hours. The end result: fewer repairs, low downtime and high productivity.
Additional Magnaplate HCR properties include:
- A coefficient of friction as low as 0.09.
- Hardness up to 48 Rc.
- Mold release.
- Permanent dry lubricity.
- Chemical resistance.
- Excellent dielectric/insulator properties.
Let Us Recommend Your Next Coating
The metal components used in embroidery machines and other industrial equipment share a common thread: the need to withstand corrosion, wear, friction and other threats. Engineered coatings solve these challenges, offering corrosion and wear resistance, hardness, dry lubrication and protection from abrasion, galling, seizing and sticking for metals like aluminum, titanium and magnesium substrates.
Be sure to contact a Magnaplate specialist to recommend an engineered coating that’s tailored to your application.
For more information about our engineered coatings that protect against corrosion and wear, please contact us.