Coatings Technology Blog
Delivering Consistency Globally For Pharmaceutical OEM
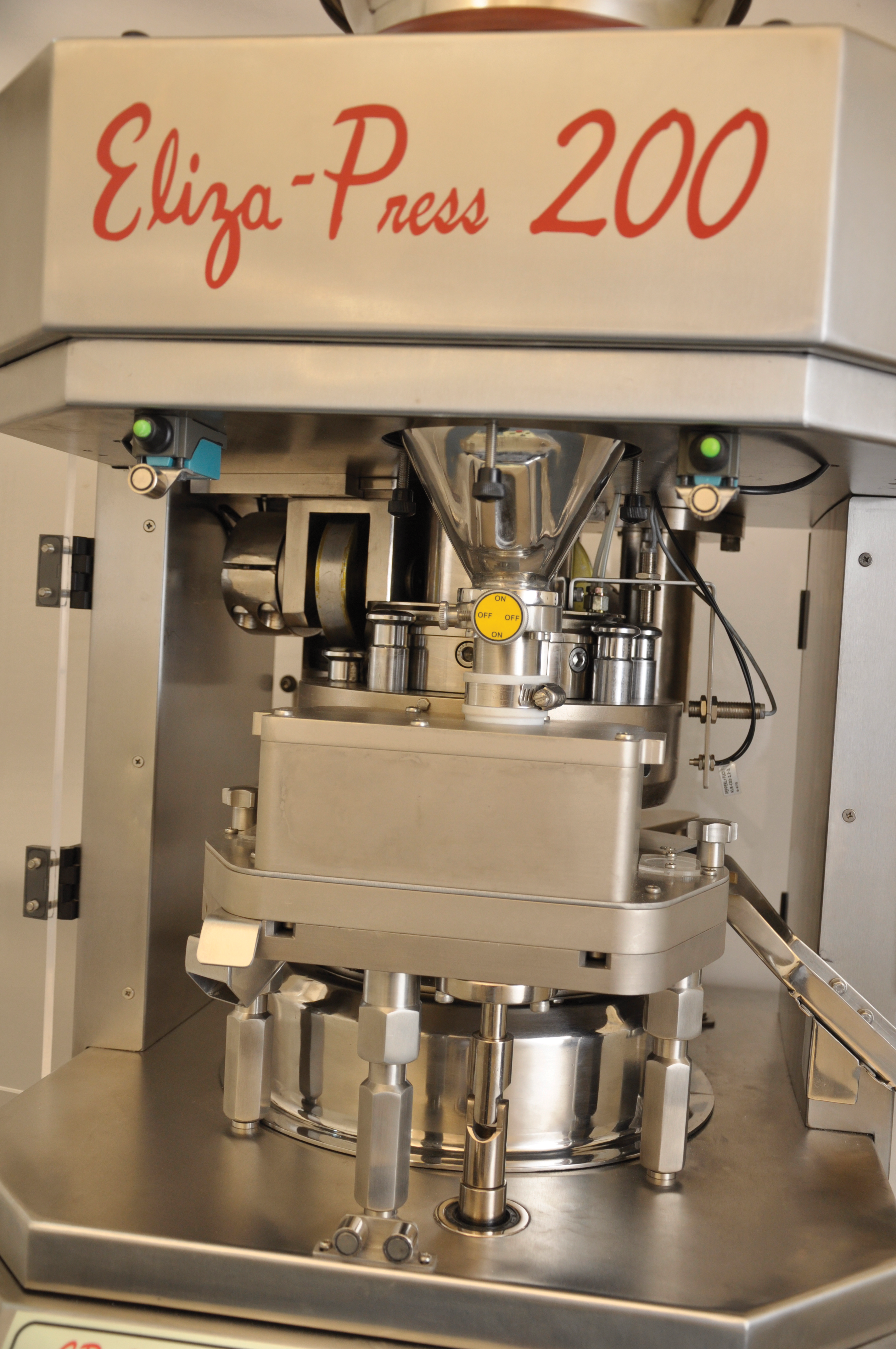
Two things make it difficult for machine builders in the pharmaceutical industry to use engineered coatings. First, many coatings in product-contact applications don’t meet FDA standards. And second, many coatings, even those that are FDA-compliant, are not available in other parts of the world—making international expansion difficult.
Nedox and Tufram overcome both challenges. Not only are they FDA-compliant, but they are also accessible worldwide. Here’s how Elizabeth-Hata, a leading manufacturer of tablet presses, recently used these coatings in its Eliza-Press rotary tableting machine.
FDA Compliance. Because Nedox® and Tufram® are FDA-compliant, Elizabeth-Hata used them to coat the aluminum and stainless-steel parts of its rotary press machine, which compresses powdered pharmaceuticals into tablets at pressures up to 20 tons. The coated parts, which include a powder feeder, scrapers and turrets, routinely come into contact with products and are particularly susceptible to wear.
- Tufram HO. To coat the feeder, scrapers, deck plates and other aluminum parts, engineers utilized Tufram HO. This coating creates a dry-lubricated surface with hardness levels between 40 and 50 Rc—protecting parts from wear, corrosion, sticking and galling. Tufram HO also provides good release properties relative to the powder.
- Nedox SF-2. To protect the stainless-steel turret that holds the die and punches from wear and corrosion, engineers used Nedox SF-2. With its wide operating temperature (-250° to +550°F), surface hardness up to Rc 68, chemical, acid and alkaline resistance and self-lubricating surface characteristics, it also exceeds the physical properties of many other common industry coatings.
Global Availability. Not only are Nedox and Tufram FDA-compliant, but they are also accessible worldwide—making international growth not just a possibility, but a reality. After expanding its manufacturing operations to India in 2008, Elizabeth-Hata required technologies that were available regardless of manufacturing location. This need factored into the company’s coating selections, as Magnaplate has licensed its coatings to partners around the world.