Coatings Technology Blog
Applying TUFRAM® To Aluminum Dies Improves Productivity For Custom Extruder
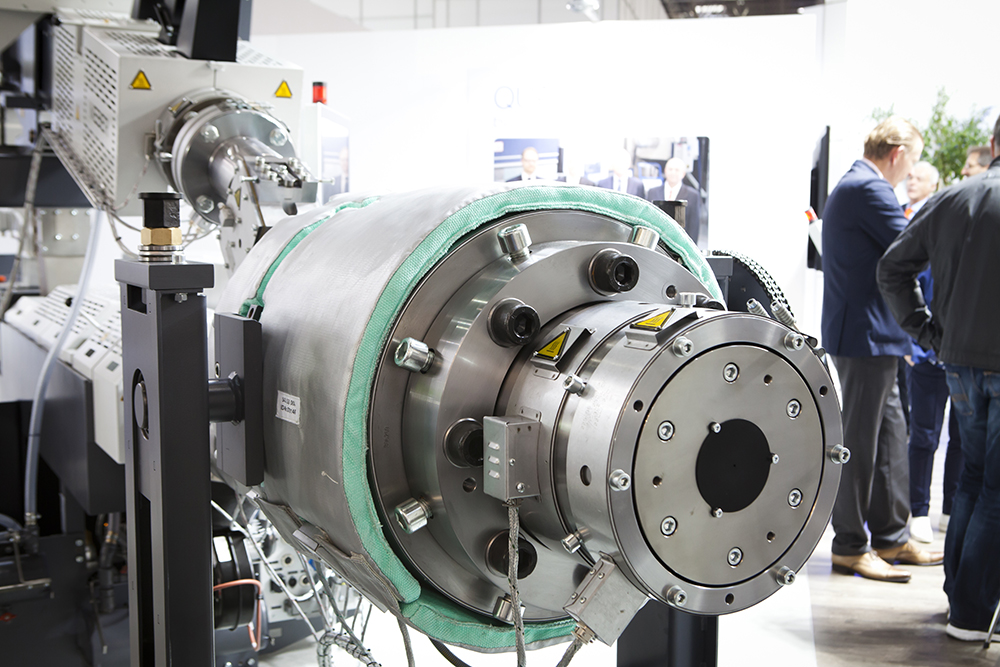
Abrasive materials used in some manufacturing processes can create surface imperfections in your tools, leading to troublesome production delays. For example, a company that provides custom profile extrusions was experiencing frequent downtime because raw plastics were scratching its aluminum dies, causing the operators to constantly halt the operation for polishing.
Problems like this can be easily overcome using engineered coatings, such as TUFRAM. Here's how this extrusion company was able to elevate the surface finish quality of its aluminum dies to that of steel-doubling die life, decreasing downtime and increasing overall productivity.
Aluminum Die Blocks Required Polishing By Hand The company uses nine extruders to produce hundreds of plastic shapes, ranging from 0.25 to 14 inches wide and up to 10 inches in diameter. Because of this variety, the company designs roughly 150 new sizing blocks each year and supplies these extrusions to many high-profile companies in the automotive and electronics industries.
Each plastic profile that emerges from an extruder should have an unmarred finish, but the raw plastics were scratching the aluminum sizing blocks during the extrusion process. Operators would have to stop the process in order to repolish the tools by hand with an emery cloth. These frequent delays had a negative impact on both production throughput and cost.
TUFRAM Enhances Aluminum Surfaces The company found a solution in our TUFRAM® engineered coating, which imparts hardness levels between Rc 40 and 65 to aluminum surfaces. The coating also protects against scratches, blemishes, marks and scoring and performs like case-hardened steel and hard chrome plating during Taber abrasion tests. Here's what happened once engineers applied TUFRAM to the aluminum extrusion dies:
- Longer die life. Thanks to TUFRAM, the company doubled the wear life of its dies-leading to an increase in overall productivity.
- Shortened tool preparation time. Coated tools were better equipped to survive storage in-between runs and were ready for reuse with minimal preparation. Previously, when taking uncoated tools out of storage, personnel had to clean and polish the surfaces to eliminate dust and residue.
- Increased confidence. Personnel no longer worried about the dies scratching their tools and parts, and instead focused their efforts on producing high-quality profiles run to run.
- Increased productivity. Because the extrusion operation ran more smoothly, overall productivity increased and downtime decreased.