Coatings Technology Blog
Anodizing Aluminum Parts - Answers to Your Frequently Asked Questions
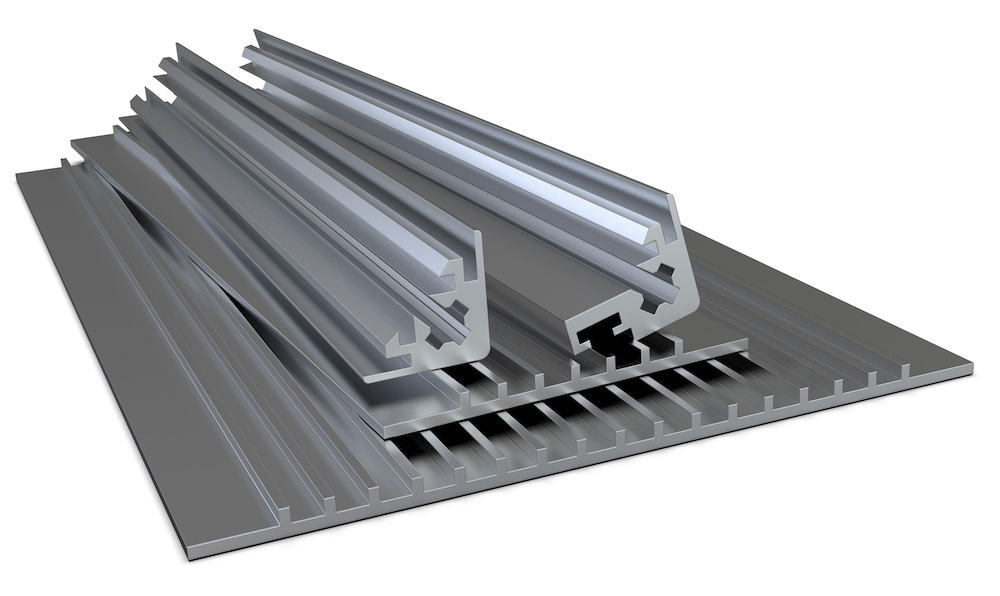
When you need to protect aluminum parts from corrosion and wear, or create a more decorative finish, anodizing is an attractive option. Anodizing can add durability to part surfaces and help extend service life. This blog post will help answer some of the basic questions you may have about anodizing aluminum parts.
What is Anodizing?
Anodizing is an electrochemical process that converts a metal surface into a durable, corrosion-resistant oxide finish. The aluminum part is immersed in an acid electrolyte bath, and an electric current is passed through the medium. Oxygen ions are released from the electrolyte and combine with the aluminum atoms of the part surface, thereby enhancing the natural oxidation of aluminum.
Are There Different Types of Anodizing?
There are three types of anodization:
- Type 1, chromic acid oxidation, creates a thin aluminum oxide film that offers good corrosion and abrasion protection. The use of chromic acid is not considered environmentally friendly, and this type is mostly employed in military and aerospace applications.
- Type 2, or “clear” anodizing, is by far the most popular anodizing method. The oxidation process is performed in a sulfuric acid bath and creates a thicker coating than with chromic acid.
- Type 3, or “hard” anodizing, is desirable for applications requiring an extra hard surface and increased oxide thickness. The process also uses sulfuric acid at much lower temperatures and higher current density that results in a much thicker and harder surface.
What If I Have a Multi-Part Assembly?
Multi-part assemblies should be anodized before assembly. Due to the strong alkaline and acids involved, studs, pins, threaded inserts or standoffs may corrode. Corroded materials in the anodizing tanks can affect current flow during electrolytic processes. In addition, gaps between components can trap chemicals and cause complications.
How Will the Shapes or Edges of My Part Affect Anodizing Quality?
In general, tighter angles are challenging. For example, the coating may not reach a 90-degree corner. C surfaces are less difficult to coat, while radiused surfaces are better to work with.
What Are the Cost Considerations?
A number of factors can influence the cost of your anodized coating. For example, hard anodizing is performed at a lower temperature and at a higher current and voltage than clear anodizing. The higher energy consumption required can add to your cost. Other factors include the time and effort required for masking and racking, the amount of rinsing needed — especially when smaller features are involved — and poor, unclear specifications can lead to additional work.
Work With Magnaplate for Consistent Quality
When you work with us to protect aluminum surfaces, you’re partnering with a company that ensures consistent anodized coating quality. For coatings like Tufram® Basic, we manage key anodizing factors such as temperatures, chemistries and amperages, and we employ an automated ramping process to ensure a uniform application every time. Our technical experts can review your application’s details, recommend the right engineered coating and determine the best anodizing process variables so your aluminum parts will perform reliably in their intended application.
For more information, contact us.