Coatings Technology Blog
Electroless Nickel Plating - Understand Your Options
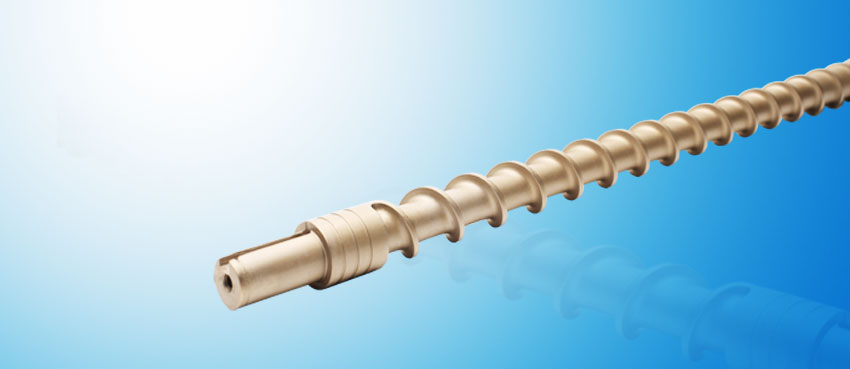
Electroless Nickel Plating: Understand Your Options
When it comes to protecting parts against corrosion and wear, electroless nickel (EN) plating has been around for a long time—in fact, more than two centuries. When evaluating surface protection methods, it’s often worth considering this tried and true process. This overview will cover the basics of electroless nickel plating and the different types available, plus advantages and disadvantages to help you make a better-informed decision.
The Basics of Electroless Nickel Plating
Electroless nickel plating is a surface treatment process that deposits a nickel alloy onto a substrate without sending electric current through the bath or the substrate. Instead, a nickel-phosphorus (NiP) or nickel-boron (NiB) alloy is introduced to a chemical reducing agent, like sodium hypophosphite, that converts the nickel ions to a nickel metal, resulting in an even deposition of metal onto the substrate. Electroless nickel plating offers many benefits such as a uniform thickness, protection against corrosion and wear, excellent lubricity, magnetic properties and solderability. The process is also used to coat non-conductive materials. Electroless nickel's wide range of applications includes computers, electronics, automotive, machinery, oil and chemical equipment, printing and food processing.
Common electroless nickel coatings are categorized by their percentage of a given mineral in the alloy by weight. The most common types are summarized here:
- Low phosphorus (1 to 4% weight phosphorus). With an as-plated hardness from 58 to 62 Rc, low phosphorus electroless nickel provides excellent wear resistance, good corrosion resistance in alkaline conditions and has a high melting point. Deposits are compressively stressed, and the coating can be soldered easily. It is typically more expensive than medium and high-phosphorus electroless nickel.
- Medium phosphorus (5 to 9% weight phosphorus). Offering good corrosion resistance in both alkaline and acidic conditions, medium phosphorus electroless nickel exhibits as-plated hardness from 45 to 57 Rc, is heat treatable to 65 to 70 Rc and has a fast deposition rate of 18 to 25 µm per hour.
- High phosphorus (10 to 13% weight phosphorus). This non-magnetic coating is well-suited to resist corrosion in severe environments. Benefits include high thickness, excellent diffusion barrier, ductility and stain resistance. High phosphorus electroless nickel solders easily and is very polishable.
- Electroless nickel boron (0.25 to 6% weight boron). Offering an as-plated hardness from 55 to 65 Rc, this typically expensive coating provides superior wear resistance, a very high melting point, excellent conductivity and it can be soldered easily.
- Composites. PTFE, hexagonal boron nitride, cubic boron nitride, silicon carbide, aluminum oxide, diamond and others.
Electroless nickel plating is not without its disadvantages. As electroless nickel baths age, contaminants may build in the solution, plating rates may reduce, phosphorus content may rise, and the deposits can develop more internal stresses or become more porous. During deposition, other factors like temperature, pH and surface area can also adversely affect coating quality. In fact, a host of problems are possible such as edge pullback, pitting, roughness, white-out, slow deposition and dullness.
Weigh Electroless Nickel Plating Against All Your Coating Options
As you consider electroless nickel plating among your surface protection options, be sure to understand the properties of each type of coating and the intentional and unintentional results of the process in order to select the best approach. If you are unsure as to whether electroless nickel plating is right for your application, take your requirements to Magnaplate. Our nickel-based Nedox® coating is formulated to exceed the physical properties of common industry coatings.
For more information about electroless nickel plating or Magnaplate’s broad range of engineered coatings, contact us.