Coatings Technology Blog
Preventing Component Wear Starts With Understanding Coefficient of Friction
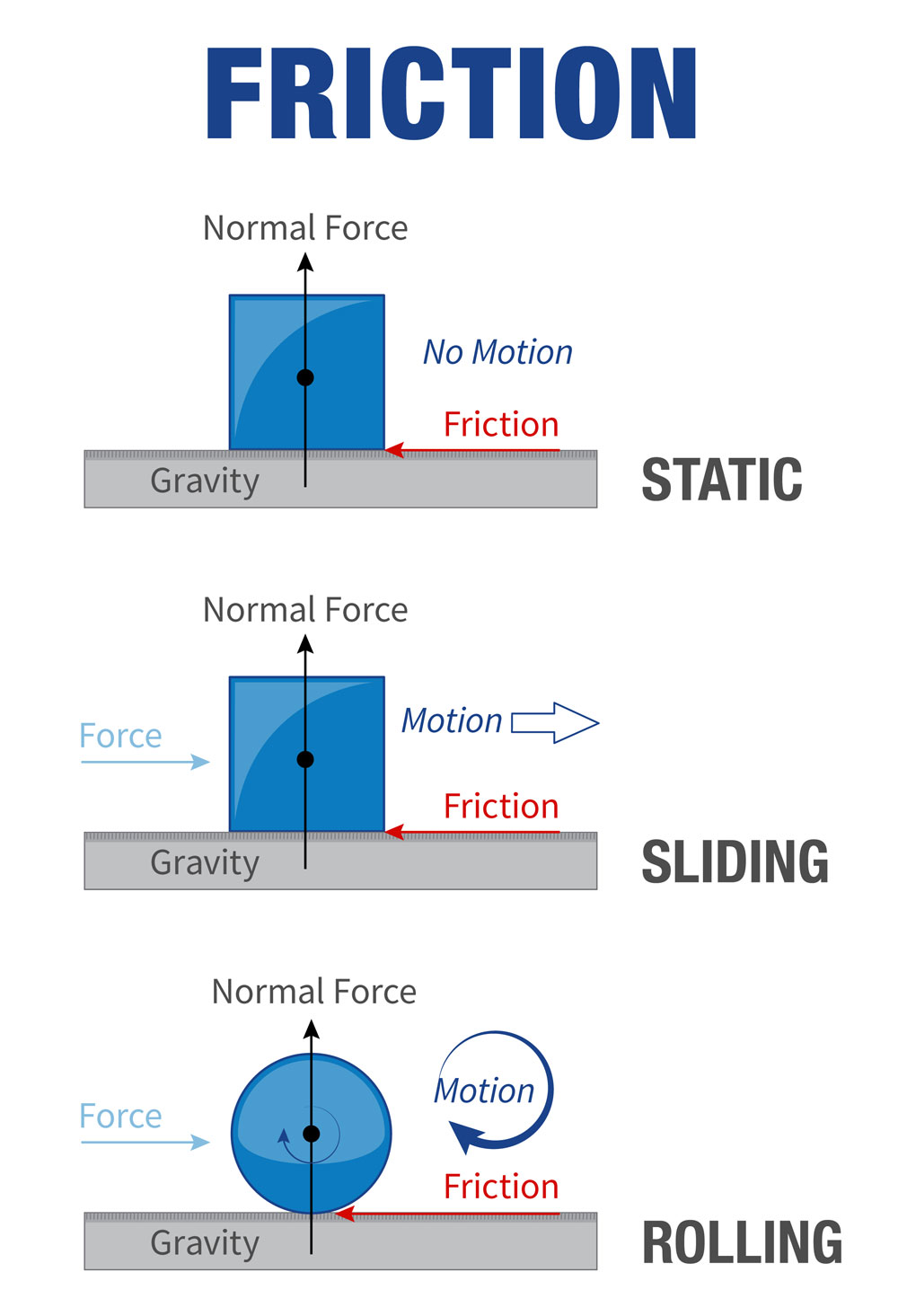
When two objects make contact with each other, there's going to be resistance, or friction, between the surfaces. Friction causes wear and affects the performance and operating life of components, so it’s important to minimize it. Although there’s no way to predict friction behavior with 100 percent certainty, understanding the coefficient of friction (COF) of surface materials is critical when developing mitigation strategies for your parts.
What Is Coefficient of Friction?
COF is a ratio of the force required to move one material over another to the total force pressing the surfaces together. It's expressed as two numbers: the static friction, or force, needed to start the movement, as well as kinetic friction, or the force required to move the object once it's in motion.
In order to reduce sliding wear caused by friction, you need a strategy to lower COF, minimizing wear and saving energy since a lower COF means less force is needed to move the components. Because two surfaces with the same hardness wearing against each other can deteriorate under modest loads, the generally accepted approach is to make one surface harder than the other. Options can range from oil and grease lubricants to advanced surface enhancement coatings.
Engineered Coatings Minimize COF
COF is as important as any other material property when it comes to reducing wear and can help you determine the best coating to choose for your parts. A coating that provides the right balance of hardness and COF can help surfaces move and slide with greater ease, leading to less wear and abrasion. The right engineered coating can also:
- Make your parts last longer and perform better.
- Lower cost-per-unit (CPU).
- Reduce downtime for maintenance or replacement.
COF Measurement and Analysis—and the Importance of Working With the Right Coating Provider
Engineers can refer to handbooks that list COF for one surface versus another. There are also various tests and instruments to measure it. In a typical instrument, one sample material is placed on a test bed as the base material, and a second sample material is placed over the first. A constant weight is applied to represent the normal force. One piece is fixed, while a gradually increasing force is applied to the second sample until the samples begin to slip against one another. Electronic force gauges measure the forces that determine static and dynamic COF, and the results are usually based on an average of multiple readings.
As mentioned above, there is no precise way to analyze friction. Existing methods cannot fully account for real-world conditions that can change friction behavior such as the application’s loading stresses, temperatures, micro finish and environment. The most effective tool to analyze and predict friction is experience, and one of the best ways to find that experience is to contact a trusted surface enhancement coating provider.
At General Magnaplate, we understand the properties of surface materials and conduct COF tests using an advanced slip and friction test instrument. Using this data, along with the information you provide about your application, we can help you select the best coating to improve the service life of your mating components.
For more information about our COF testing and analysis or about our broad range of engineered coatings, contact us.